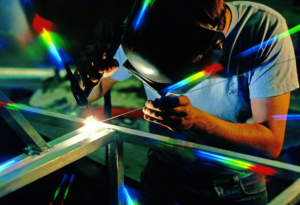
Businova, a 100% connected bus
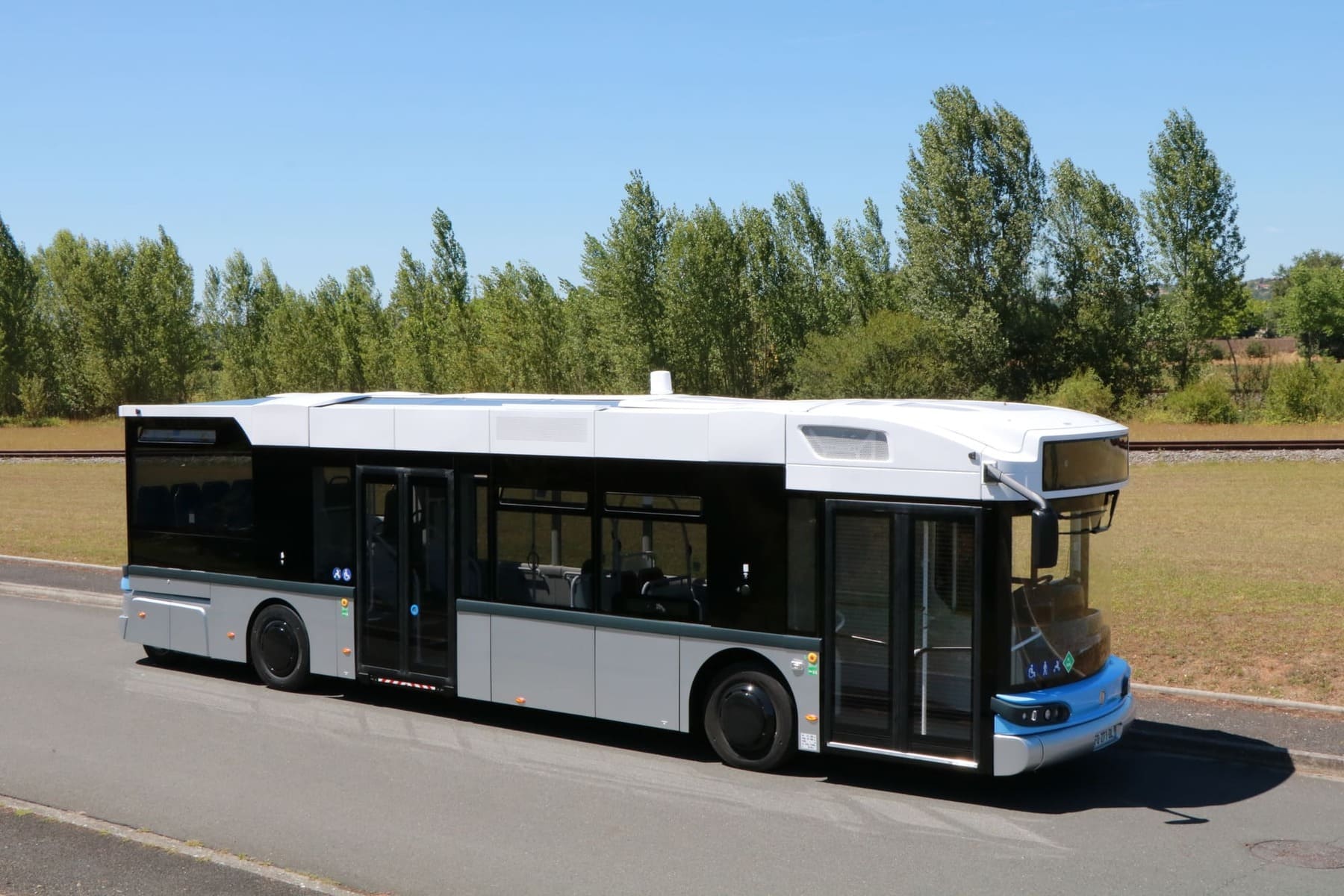
Bus connectivity is now a major competitive advantage. It allows the operator to meet its economic needs and interests, to ensure the comfort and safety of the drivers, but also, as an option, to offer the increasingly connected passengers free access to the internet during their travel time. All of our Businova vehicles are equipped with connected boxes that, thanks to the ascending data, allow for real-time monitoring of the operation and performance of each bus, control of the drivers’ start and end of service, anticipation of failures thanks to predictive maintenance, and remote diagnosis in case of problems.
Real-time operation monitoring
The data recorded by the bus allows for the generation of real-time metrics and the construction of reports adapted to the operator’s interests on his fleet of vehicles. Depending on the need, emails, notifications and even a web page provide information on the Businova’s range, average speed and consumption. Equipped with GPS, it is also possible to trace their routes and know their exact position in real time. This is a considerable advantage for both the operator and the maintenance teams in the event of a breakdown.
Control of service start/end and performance monitoring
Passenger transport is one of the most regulated activities in terms of working hours. The connectivity of the bus makes it possible to easily control the start and end of service, break times and the drivers’ shifts. This is a real convenience for the operator. All driving data (speed, acceleration, braking, gradient, temperature, etc.) is also obtained for each driver and their level of eco-driving can therefore be easily analyzed in real time. This feature allows the operator to efficiently analyze the performance of his fleet and optimize its operation.
Eco-driving of drivers
Thanks to the analysis of driving data, we can set up internal training sessions to improve the eco-driving of drivers and thus the performance of the Businova. This is an on-demand service offered by SAFRA Manufacturer: it allows to learn how to recover energy during braking by anticipating the hazards of the journey.
Predictive maintenance
The main advantage of predictive maintenance is to anticipate the failure of a vehicle before the problem appears. Thanks to the data collected in real time, it is possible to analyze any abnormal change in the behavior of a system compared to its history. In the form of a notification, the information is sent to the respective interfaces of the SAFRA Manufacturer and the customer, who can decide what action to take and plan an intervention.
Example: daily/weekly/monthly (depending on the request), an email is sent to the operator to inform him of the changes observed on the vehicles. The after-sales service can, for example, warn him that the tire pressure of a given vehicle is too low and that he should plan to inflate it the following week.
In addition, if a system fails repeatedly after a certain number of kilometers, or years, we have the ability to repair it and anticipate the date of the next possible failure. We can then schedule preventive maintenance on the component in question.
Remote diagnosis
In the event of a problem or breakdown, remote diagnosis is a real convenience for the driver or maintenance agent. During operation or at the depot, remote access to the vehicle’s data allows the driver to see, in real time, where the failure is occurring.
Example: a driver calls the service department because the vehicle is not moving. The service department then connects to the vehicle remotely, performs a diagnosis and finds a solution to the problem: “It seems that the handbrake is on, is the LED active? The driver answers no, releases the brake and the vehicle moves again: we know that the problem is with the LED.
Interview with Florent Andrieu, Head of Remote Diagnostics and Performance Optimization at SAFRA Manufacturer.
“All Businova vehicles are equipped with connected boxes that collect, process and transmit vehicle data. Geolocation information is retrieved via the box’s GPS. For the others, it is the CAN bus (standard and extended) that communicates directly with the hundreds of sensors present on the vehicle. All these data are then concatenated, then stored on the SD card of the box and transmitted to the server thanks to an integrated SIM card. The transmission is done via the GSM network (Edge/3G/4G) using a specific protocol (MQTT).
In the server, the data are retrieved by a software (MQTT broker), then stored in a database (InfluxDB) allowing the management of metrics and events. They are also transmitted to two different interfaces: an external interface that can be used directly by the customer and our internal interface SAFRA Constructeur.
On the external interface, the data are transmitted via a specific protocol (TiGR implemented by ITxPT) (integrate symbol). This protocol allows to report events throughout the day in the form of notifications with a standardized format (beginning/end of day, defects, consumption, engine running time, etc.). These notifications can then be used directly by the customer.
At the same time, the data is fed in the form of graphs to our internal after-sales service interface, which is built on several levels: first, with a global view of the different cities where the Businova buses circulate; then, with a tab for each city, where the route and current position of each bus in the fleet can be observed; finally, with a page listing all the data specific to a given Businova. On the global view of the Businova in question, one can thus observe the performance, defects or eco-driving tracking of the driver in real time. Another section also allows you to view data by system (compressor, thermal engine, driving position, ABS, suspension, etc.).
Each customer is given access rights to our interface. This interface can be customized according to the operator’s needs and requirements.
"If you are an operator with your own Fleet Management System (FMS), a standardized interface is also available. SAFRA has developed the Businova© with the constant concern of not being a captive solution and remaining an open system for the operator. Thus, our company is totally transparent about the vehicle data. The list of transmitted data (mileage, speed, engine speed, etc.) is always established according to your wishes".
A word from Alexandre Taurines, Project Manager, SAFRA Constructor
In a world facing ever more pressing environmental issues, transition
“A stone has no hope of being anything other than
The fourth leading cause of mortality in the world, air